In 21 century, energy-saving and consumption reduction have become a hot topic of global concern. Governments around the world have formulated many regulations on energy conservation, exhaust emission, and noise reduction. For the machinery industry, the most effective way to save energy and reduce emissions is to decrease the weight of machinery, and aluminum alloy plays an extremely important role in it which in a way, reducing the energy consumption. Aluminum alloy is considered to be the future green material with the most abundant development and application potential in the 21st century.
Tianhe Casting Group now has different cold and hot chamber processing equipment, metallographic, physicochemical, and mechanical testing equipment, with an annual production capacity of 7,000 tons of non-ferrous castings. With our company's high adoption to market demand and continuously launching of new products, the range of products has increased from less than 100 kinds at the beginning, to 177 , including engine parts, transmission parts, tube parts, and body frame products for commercial vehicles, and now we are also developing safety parts for electric and electric- oil mixed vehicles. Our leading products are 360CS10/S20 product series and pump body series, all of which are made of metal type cast alloy.
We successfully passed ISO9001 quality system certification in January 2004, and ISO/TS 16949:2002 quality system certification in February 2008. Furthermore, we got IATF 16949:2016 quality system certification in 2016. Our company has successfully utilized the five tools, seven steps, etc as our quality control methods. In order to show our determination to maintain a high-quality working and living environment for our workers and future generation. We have also passed ISO14001:2015 Environmental Management System and ISO 45001:2018 health and safety (OH&S) management system. We are actively checking the implementation of 6S management, which provides management and organizational assurance for manufacturing products that satisfy customers. We are well received by customers and have been awarded as a "Quality Trustworthy Supporting Factory" by our major customers many times because of our stable product quality.
n 2014, the casting division of Tianhe Casting Group was relatively backward due to the production process. The heat generated by casting was not utilized, the penetration rate of clean production equipment and raw and auxiliary materials was not enough, and pollutant emissions were huge. There were no effective terminal treatment facilities and sand regeneration and reuse facilities, therefore a large amount of waste sand was treated as general garbage, and the comprehensive utilization rate of resources was low.
Before the implementation of the project, the main product of the company was the production of iron castings by the investment casting process. The process includes mold design, mold making, tree grouping, shell making, dewaxing, roasting, smelting and pouring, sand cleaning, heat treatment, straightening, machining, etc. The process flow is shown in the Figure below. Features are longer process, more complex quality control process, long manufacturing cycle, weak production strain, labor-intensive, more difficult to automate production, and high energy consumption. The original investment casting process method is far from being able to adapt to the modern development needs of energy-saving, environmental protection, and green casting.
The benefits of casting sand recycling are as follows.
First, the surface is made of sand whose refractoriness, density, surface quality, permeability and other properties are better, so the rough casts will come out with low surface roughness, high dimensional accuracy, casting size accuracy and surface roughness can reach CT5 ~ CT7, Ra-6.3 ~ 12.5 um, close to or even reach the level of investment casting. The machining allowance is at most 1.5~2 mm, which can greatly reduce the cost of machining, and compared with the traditional sand casting method, it can reduce the machining time by 40% to 50%.
Second, a large number of sand using recycled sand to gain a more compact structure. No binder is needed for making the sand mould, the casting production process is simplified, and labor productivity is higher. The moisture of the sand is greatly reduced which in a way, reduces the adverse effects of sand treatment and recycling on the quality of castings, and simplifies the sand treatment process. Almost all the sand can be reused, saving costs. Therefore, the production efficiency is greatly improved, which is conducive to the automated production of large quantities.
Thirdly, using recycled sand is benefiting a cleaner working and living environment. The use of polystyrene (EPS) and other plastic foam to make foam mold samples, and investment casting generates a large amount of gas and fumes, causing serious environmental pollution. In contrast, the decomposition gas is relatively small during the casting of the reused sand casting and is concentrated in the sandbox to facilitate the treatment of negative pressure suction type combustion purifier. Compared with the traditional casting method, CO gas and silica dust hazards were significantly reduced, the environment was improved, easy to achieve mechanization, automation, and clean production.
Fourthly, dust removal system is equipped throughout production, from the process of furnace melting to moulding, pouring, sand dropping, and sand regeneration, which solves the drawbacks of poor labor conditions in the traditional casting line, and combines with the actual enterprise, energy-saving and emission reduction measures, minimizing electric and water resources usage, making full use of waste heat to reduce energy consumption and improve economic efficiency.
Around energy saving and emission reduction, the casting division reconstruction will focus on eight aspects, through systematic optimization of design, the introduction of casting frontier production technology, improve the enterprise production intelligence level, achieving electricity saving, water saving, reusing waste heat, reducing waste discharge and comprehensive management capacity, improve the workers' working environment, etc. The relationship between energy-saving technical measures and recycling transformation is shown in Figure below.
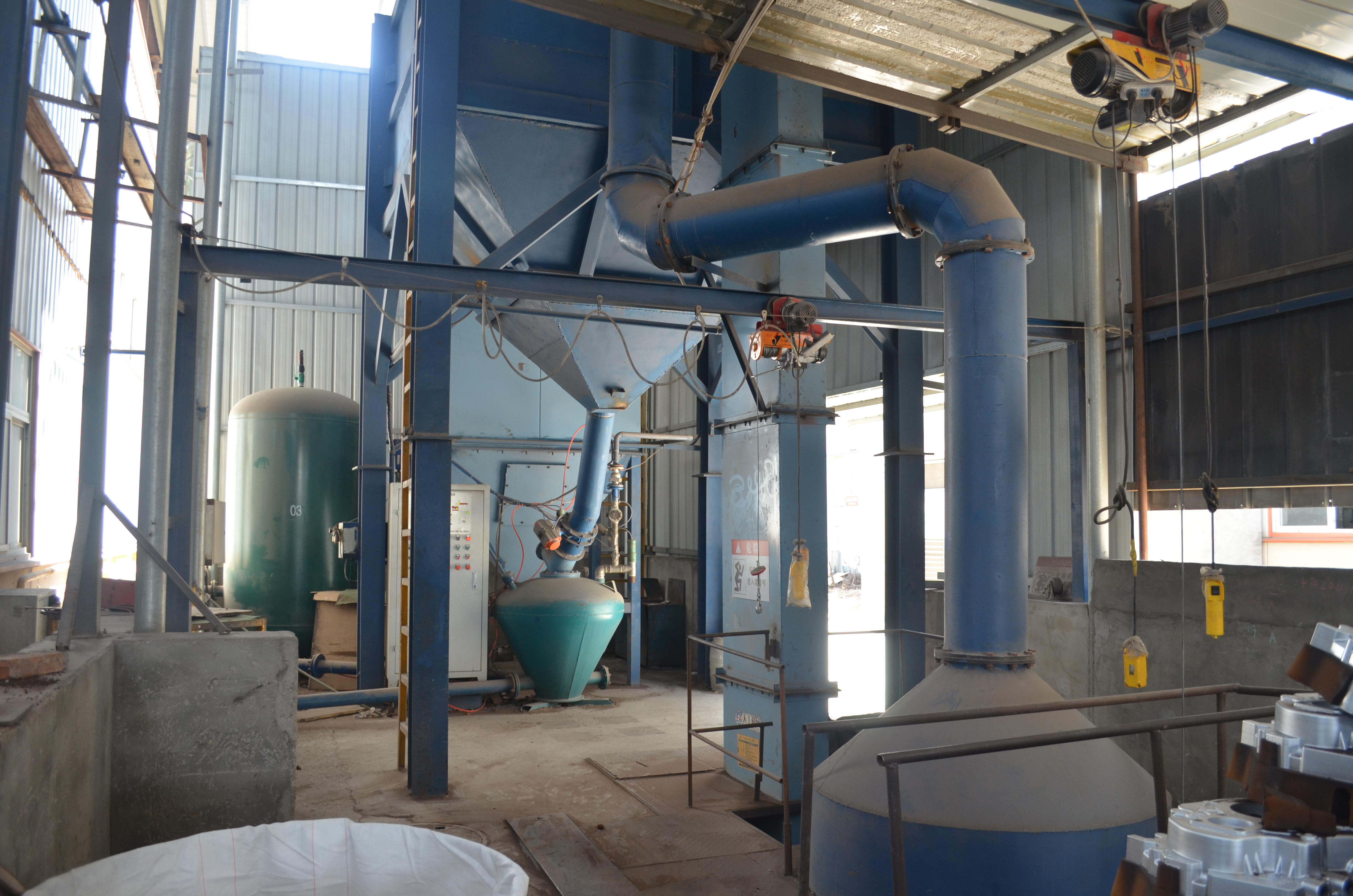
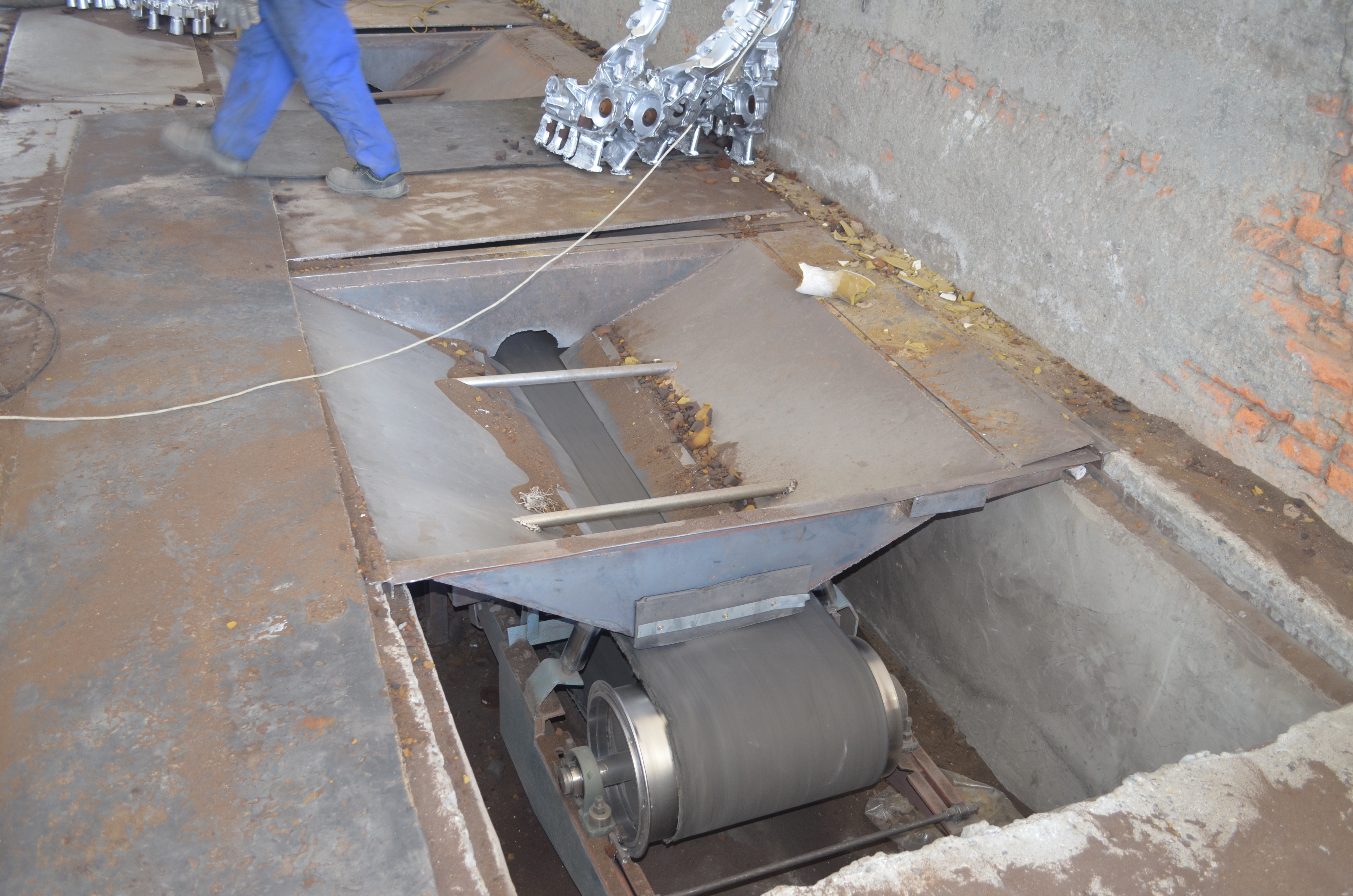
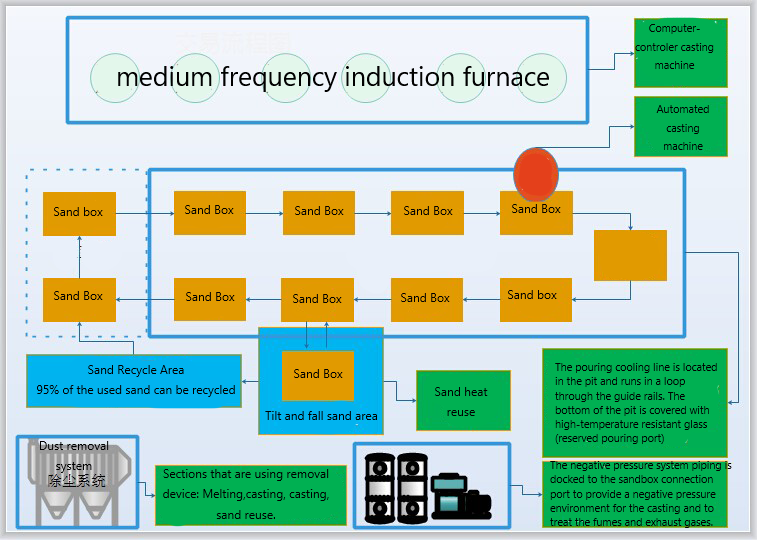
进入21世纪后,节能降耗成为全球关注的热点话题,世界各国政府先后制订了关于能源保护、废气排放、降低噪音和安全保障等许多法规。对于机械行业来说,节约能源、减少排放的最有效办法就是减轻机械的自重,而铝合金在机械的轻量化中扮演着极为重要的角色,被认为是21世纪最富于开发和最有应用潜力的“绿色材料”。
公司现冷热加工设备、金相、理化和力学检测设备齐全,具备年产有色铸件7000吨的生产能力。由于我公司能适应市场需求不断推出新产品,产品品种从最初不足一百种上升到177种,包括商用汽车的发动机件,变速箱件,管类件和车身车架产品,目前也在进行新能源汽车的配套安全件的开发。我公司主导产品为360CS10/S20产品系列和泵体系列,所有产品材质均为金属型铸造合金。
2004年1月份顺利通过ISO9001质量体系认证,2008年2月份顺利通过ISO/TS 16949:2002质量体系认证,2016年拿到了IATF 16949:2016质量体系认证。同时,为了提升环境绩效和保证工人的职业安全水平,我司通过了ISO45001:2018 和 ISO14001:2016。我公司成功运用了五大工具、七步法等,并积极推行6S现场管理,为生产用户满意的产品提供了管理及组织保证。因我公司的产品质量稳定,受用户好评,多次被主要客户评为“质量信得过配套厂”。
覆膜砂回收的好处有以下几点。
第一,面砂为覆膜砂硬化壳层,其耐火度、致密度、表面质量、透气性等性能均较好,因此,所生产的铸件表面粗糙度低,尺寸精度高,铸件尺寸精度和表面粗糙度分别可达到CT5~CT7、Ra-6.3~12.5 um,接近甚至达到熔模铸造水平。加工余量最多为1.5~2 mm,可大大减少机械加工的费用,和传统砂型铸造方法相比,可以减少40%至50%的机械加工时间。
第二,大量背砂采用再生砂紧实造型,无粘结剂,铸件生产工序简化,劳动生产率高。型砂水分大大减少,减少了砂处理回收再用对铸件质量的不良影响,并简化了砂处理过程。型砂几乎可全部回用,节省了成本。因此,生产效率大大提高,有利于大批量自动化生产。
第三,容易实现清洁生产。相对于消失模铸造,使用聚苯乙烯(EPS)等塑料泡沫制作泡沫模样,浇注时排出的大量气体和烟尘,对环境污染较严重。而覆膜砂壳型浇注时分解气体相对较少,且集中于砂箱内便于负压抽吸式燃烧净化器处理。与传统铸造方法相比,项目中工艺噪声、CO气体和硅石粉尘危害明显减少,环境显著改善,易实现机械化、自动化和清洁生产。
第四,覆膜砂闭环分离式全自动生产线配备了除尘系统,对电炉熔炼、造型、浇注、落砂、覆膜砂再生等工序均采取除尘措施,解决了传统铸造行劳动条件差的弊病,并结合企业实际,对电能、水资源采取节能减排措施,充分利用余热减少能源消耗,提高了经济效益。
围绕节能减排,车间建设将重点从八个方面开展工作,通过系统地优化设计,引进铸造前沿生产技术,提升企业生产智能化水平,达到节电、节水、余热再利用、减少废弃物排放以及综合治理能力,改善工人作业环境等。节能技术措施和循环化改造关系如图2:
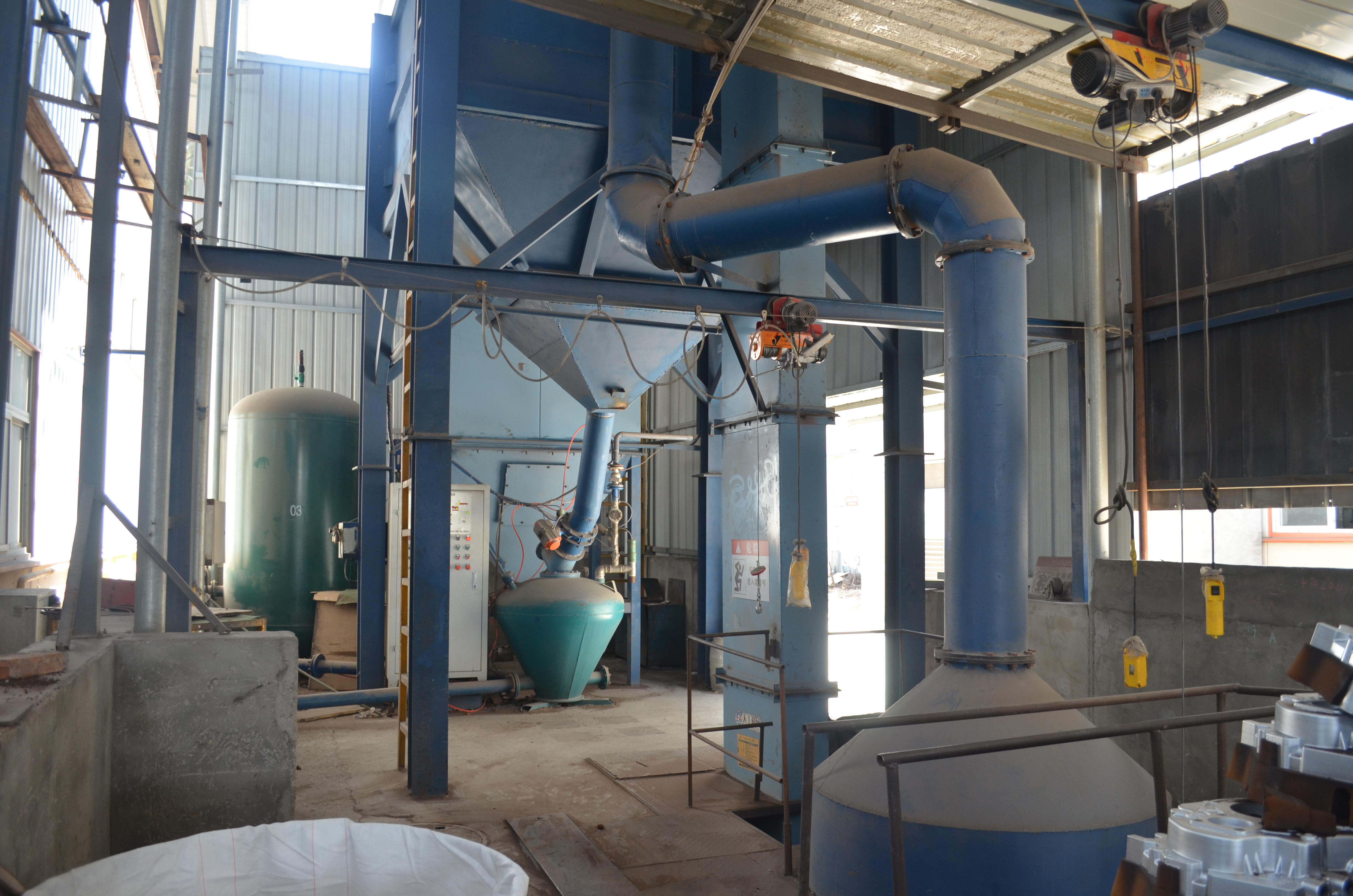
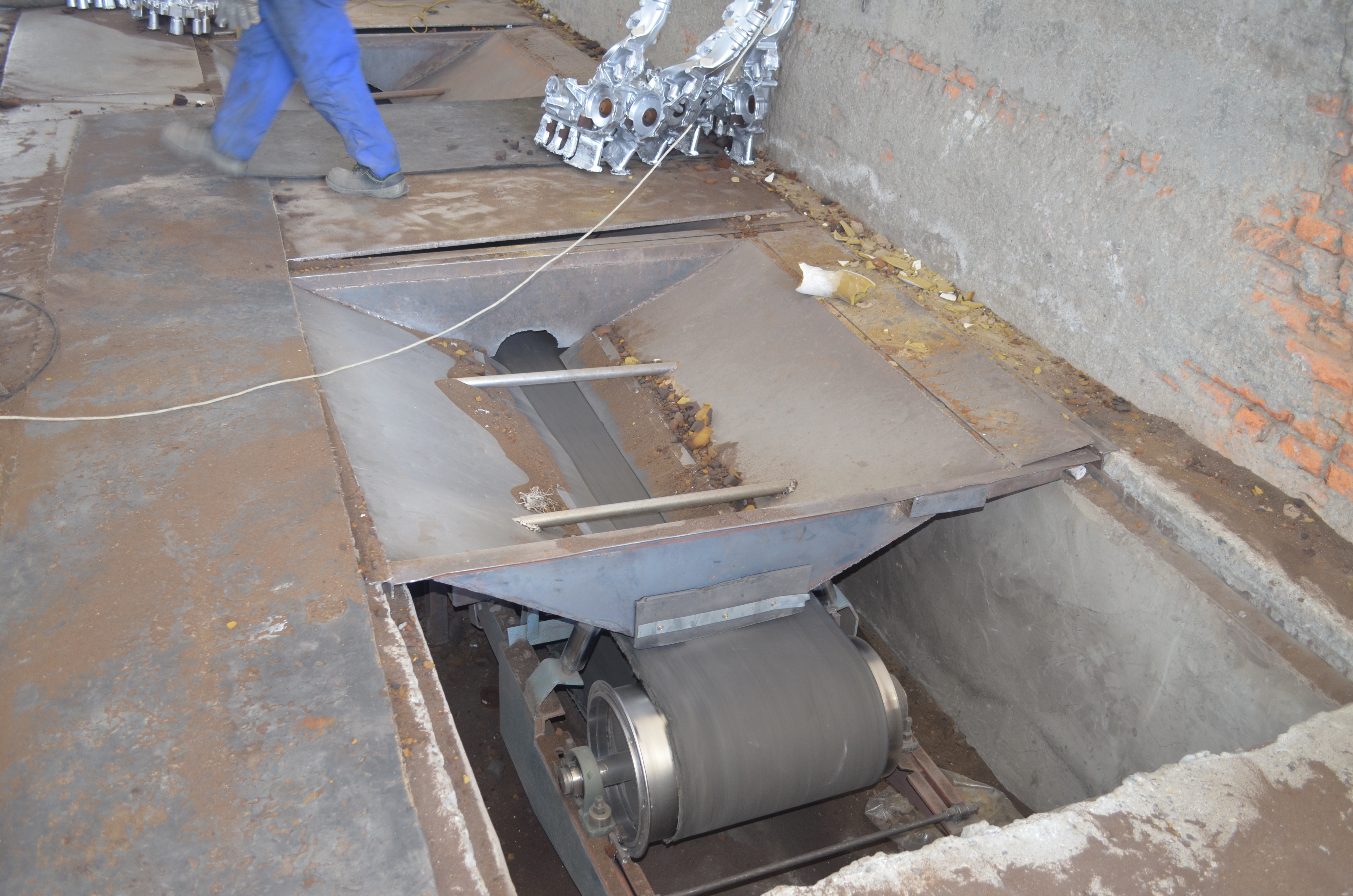
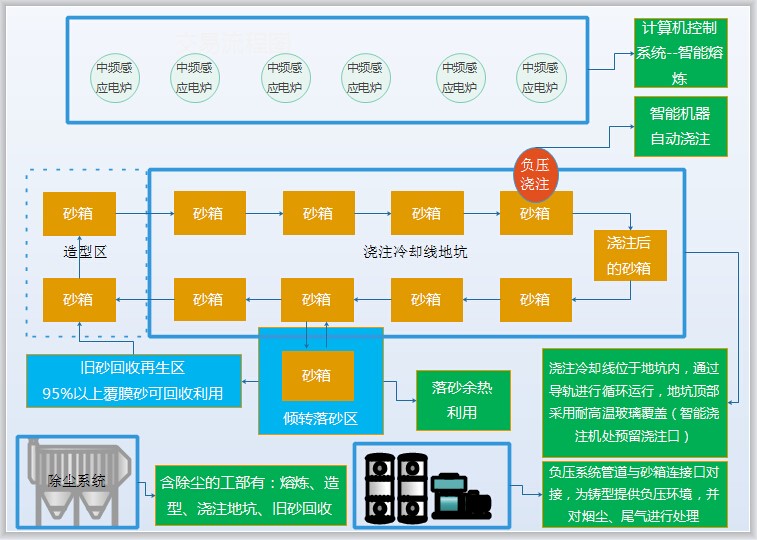
Post time: May-07-2022