The steering knuckle, which is also known as the ram's horn, is mainly located on the steering axle of the car and is one of the most important parts of the steering.
It allows the vehicle to receive the directional instructions from the steering wheel in a stable and flexible manner, and also bears the load brought by the front of the car, so the production requirements are high enough in strength.
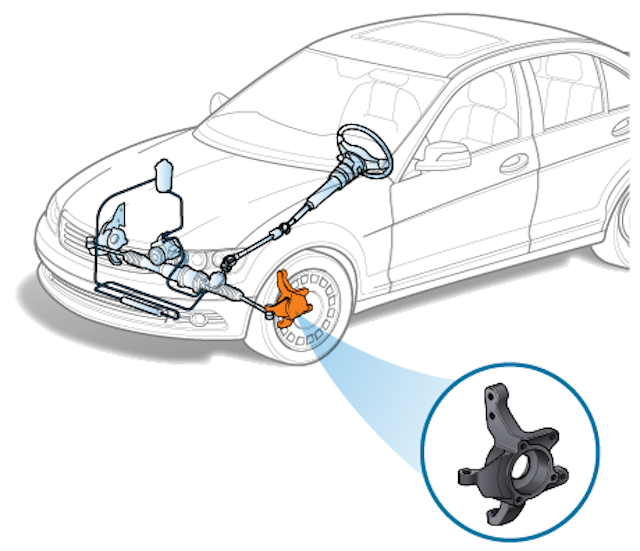
Deyang Tianhe Casting Group is currently undertaking two types of steering knuckle casting process, one for the front and one for the rear. Both products are used on electric cars.
The steering knuckle is an important safety part in the chassis system of a car.
It is also an extremely complex shaped part, which requires high mechanical properties, and dimensional and positional accuracy.
In order to ensure the performance of the safety parts, Deyang Tianhe Casting Group introduced an automatically gradable X-ray flaw detector from UNICOMP at the customer's request.
In the casting process such as improper operation, production process, structure and raw materials can cause defects such as porosity, looseness, air bubbles and inclusions.
Any problem in any part of the process can lead to defects within the casting and affect its quality, X-ray non-destructive testing technology has become a powerful tool for judging the quality of castings.
X-ray digital imaging inspection equipment for castings, equipped with the latest digital detectors and high-definition image processing technology, is suitable for both sampling and full inspection and meets the task of non-destructive, high-quality inspection of a wide range of materials, such as steel, aluminium, ceramics, composite materials or rubber and other different materials.
It fully meets the requirements set out in national standards regarding radiographic inspection image quality, system characteristics, ionising radiation protection and industrial X-ray flaw detection.
X-ray testing machine in Tianhe Casting Group
The X-ray tube emits X-rays, which penetrate the object under test. Depending on the different densities and thicknesses of the object under test, the imager converts the X-ray information penetrating the object under test into grey-scale information and transmits it to the computer.
The computer's rating software will process the original image through image processing software to reduce noise and sharpen the image so that the internal structure of the object to be detected can be clearly displayed.
According to our technical analysis of the size, appearance, density, maximum thickness and testing efficiency of the user's test workpiece, the rotary table structure is used.
The inspection workpiece is placed on the turntable. The inspection system meets the user's workpiece inspection. For standard workpieces, automatic inspection can be achieved. The turnable work table is used for loading and unloading, and the upper and lower translucent inspection mechanism, as shown in the figure below:
The robot arm is capable of 360 turnings, in order to examine the product from different angles.
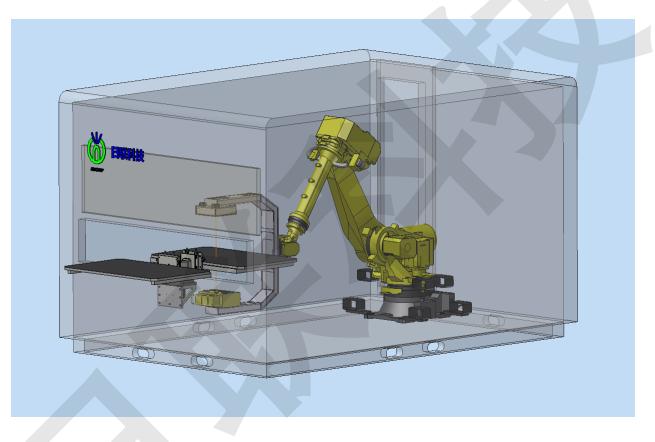
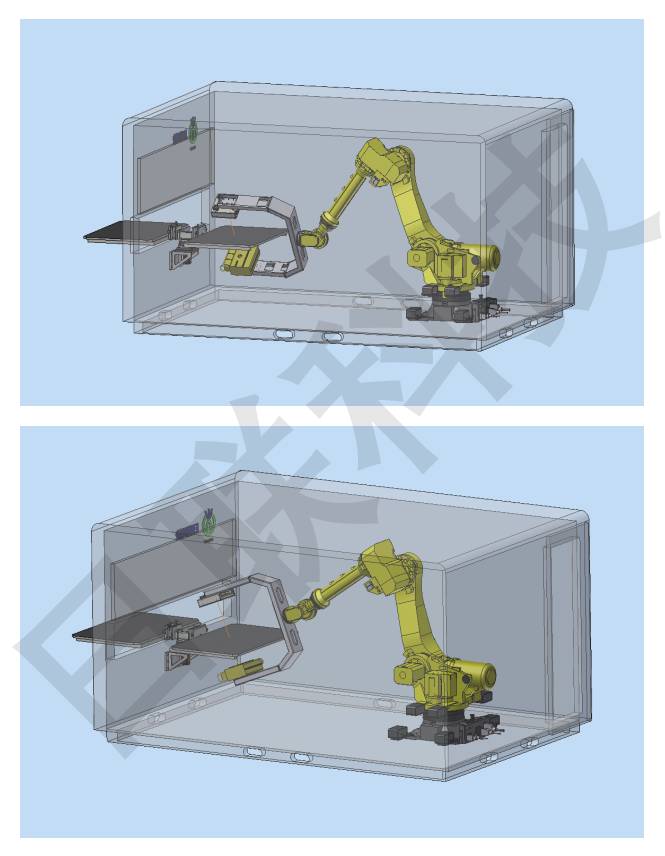
The loading table can be rotated 180 degrees, which can realize the synchronization of material loading and detection, and improve the detection efficiency. The loading table is made of materials with low density which does not affect the imaging quality when the product is placed on the loading table. The pallet can also be equipped with a fixture tool, and the special-shaped workpiece can be used. Fixtures are fixated to achieve the best imaging results.
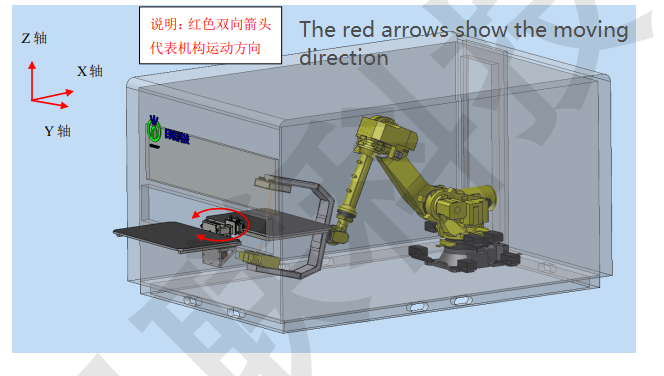
Therefore, X-Ray testing is the best nondestructive inspection method for detecting internal defects of castings. The pictures below are some real-life testing images taken by the X-RAY testing machine.
Post time: Aug-05-2022